Edgebanding Troubleshooting Tips
Edgebanding pulls off easily by hand. Hot melt Adhesive remains on the chipboard. The grid pattern of the glue application roller is visible
- Not enough adhesive applied
- Room temperature too low
- Edgebanding material too cold (stored outdoors)
- Hot melt Adhesive temperature too low
- Feed rate too low
- Too little pressure applied by application roller
Edgebanding pulls off easily by hand. Hot melt Adhesive remains on the chipboard. Hot melt Adhesive surface totally smooth (Edgebanding slips off)
- Board and/or Edgebanding too cold
- Check hot melt Adhesive type
- Check application of bonding agent
Hot melt Adhesive largely remains on the Edgebanding
- Temperature of board material too high as a result of previous processing (e.g. veneering)
Adhesive joint not closed (Edgeband gluing machine)
- Too little pressure applied
- Adhesive too cold
- Increase application temperature or preheat board or increase feed rate
- Edgebanding either not or reverse pretensioned
Glue joint not closed (machining centre)
- Too little pressure applied
- Edgebanding was fed in too cold and cannot be squeezed
- Edgebanding material restoring force too high
- Increase heater power or reduce feed rate
- Increase geometry or use a thinner Edgebanding
- Adhesive not suited for use in machine centres, adhesion under heat too low
Edgebanding is bonded only at the edges
- Too little pressure applied
- Milled joint on board hollow
- Edgebanding pretensioning too high
Inadequate bonding of the glued Edgebanding at the face side of the board, or the Edgebanding is chipped on the face side due to misaligned Adhesive application roller
- Not enough Adhesive applied due to misaligned glue application roller
- Apply more Adhesive
Milling waves are visible
- Feed rate too high
- Cutting speed of cutters too low
- Re-process with scrapers and buffing; cut against the feed
- Increase number of cutters on router bit
- Increase rpm
On thick Edgebanding the colour fades slightly in the milled areas (stress whitening)
- Warm up milled area with hot-air station (can be retro-fitted)
- Scraper blade chips too thick
- Rework on buffing station
- Reduce scraper blade chip thickness (max. 0.1 – 0.2 mm)
Evidence of stress whitening in radius during machine centre processing
- Edgebanding fed in too cold
- Increase heater power or reduce feed rate
- Increase geometry or use a thinner Edgebanding material
Adhesive stringy after application
- Reduce application temperature
- Clean gluing part
- Test using different Adhesive
So-called “mice teeth” in the joint
- Apply more Adhesive
- Increase application temperature
- Preheat board
Breakout of longitudinal edges after cross- edging
- Only format MDF board and use
- Check the router for immersion depth
- Reduce material removal or use different chipboard
Edgebanding surface print damaged during machine centre processing
- Use special rubber rollers
“Indentations” or “scratches” in the Edgebanding
- Clean Edgebanding draw-in
- Clean press rollers and spray with separating agent
- Clean scanning head; if this does not help then check scanning head for damage and replace, if necessary
Breakouts or smears at Edgebanding ends
- Sharpen cross-cut saw
- Ask the tool manufacturer for a suitable tool
Breakouts on top and bottom edges
- Reduce Edgebanding overhang
- Acclimatise Edgebanding and boards one day prior to processing (over 18°C)
- Increase room temperature and prevent draught
Edgebanding smears when copying
- Reduce number of blades
- Control rpm
- Mill Edgebanding against the feed
- Increase feed rate
3D 2in1 offset in corners
- Accurately set Edgebanding downholder
- Minimise Edgebanding overhang
- Check that Edgebanding is straight
Edgeband Finder
Looking for the perfect Edgebanding?
Make sure you use the Edgebanding Finder. You can specify size, type, material, board manufacturer, embossing and gloss level to find that perfectly matched Edgebanding!
Edgebanding Processing Information
Customer Case Studies
Quiznos uses 3D 700R Brushed Aluminum on their table tops.
Especially in high traffic areas like Quiznos restaurants, Doellken 3D Edgebanding in 2mm is superbly suited to meet the highest durability standards.
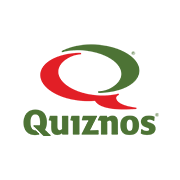
Tim Hortons uses 3D 700R Polished Chrome in their downtown restaurants.
Especially in high traffic areas that are prone to high impact, Doellken 3D Edgebanding in 2mm is suited to be long-lasting and resistant to impact. The urban-looking metallic design fits perfectly into the downtown environment.
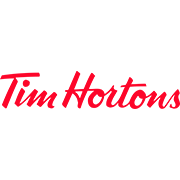
Sears uses 4803 Gowanda Maple across 500 store locations across the USA.
A nationwide renovation project requires a reliable supplier of quality edgebanding. Retail stores require high-quality, durable edgebanding solutions due to high traffic and impact.

Kohl’s uses 3179 Lakestreet Oak in their retail locations.
Kohl’s ulitilized a 3mm Woodcore pattern showing a natural looking woodgrain effect throughout the thickness of the material eliminating the ‘picture frame’ effect.
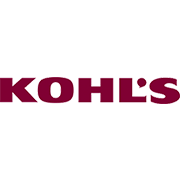
Bed, Bath and Beyond uses 7515 White edgebanding in their retail locations.
3mm thick Edgebanding was applied on all visible parts like shelvings, table tops and free-standing displays to provide a clean look with the highest durability.
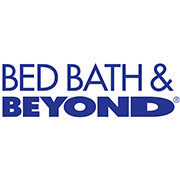
Krispy Kreme restaurants use 2001 White and 9155 Hunter Grey for their restaurant furniture.
Under the consideration of Krispy Kreme corporate colors, Doellken delivered 2mm and 3mm thick Edgebanding applied on all visible parts in a color consistent product quality.
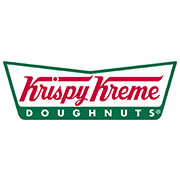
JC Penney uses 4469 Kensington Maple in their retail locations.
JC Penney found perfectly matched edgebanding to their Wilsonart 10776 board.
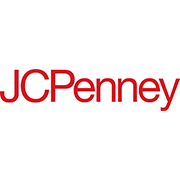
Burlington Coat Factory retail locations use 4397 Pearwood, 7309 Sage, and 6754 Blueberry Matrix.
The specified 2mm Edgebanding in Pearwood matches perfectly the laminate and significantly protects the edges of the fixtures in high traffic areas.
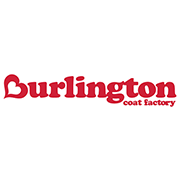